Averías en Paneles Solares
Las averías en los paneles solares son fallos que provocan una pérdida total o parcial de rendimiento, pueden generar riesgos de seguridad (por ejemplo, incendios por puntos calientes) y acortar de forma prematura la vida útil del módulo. Aunque el envejecimiento natural de un panel solar implica cierta degradación, la mayoría de las averías responden a defectos de fabricación, materiales de baja calidad o errores en la instalación y el transporte de los módulos.
Entre las causas más habituales se encuentran la calidad deficiente del BOM (Bill of Materials), que puede suponer hasta un 41% de módulos defectuosos al emplear componentes inadecuados ; el estrés térmico en entornos de altas temperaturas y humedad (pruebas de Damp Heat registran pérdidas de potencia superiores al 30% en paneles afectados) ; la exposición prolongada a la humedad, que degrada encapsulantes y backsheets; y, finalmente, una instalación inadecuada o transporte brusco, que favorece la aparición de microfisuras capaces de reducir la generación hasta un 42,8%.
Los problemas más comunes de las placas solares son los siguientes:
- Puntos calientes, o hotspots
- Microrroturas
- Destrucción del Tedlar
- Deslaminado de las células solares
- Problemas con los diodos de bypass
- Amarillamiento del EVA
- Soldaduras defectuosas
- Corrosión
- Efecto PID
- Pérdidas por calor húmedo
- Roturas de Vidrio
Contenido
- 1. Puntos calientes, o “hotspots”
- 2. Microrroturas
- 3. Destrucción del Tedlar
- 4. Deslaminado de las células solares
- 5. Problemas con los diodos de bypass
- 6. Amarillamiento del EVA
- 7. Soldaduras defectuosas
- 8. Corrosión
- 9. Efecto PID
- 10. Pérdidas por calor húmedo
- 11. Roturas de Vidrio
- ¿Se pueden reparar las placas solares dañadas?
- ¿Las averías de los paneles solares dependen de su calidad?
1. Puntos calientes, o “hotspots”
Los puntos calientes son zonas defectuosas dentro de un módulo fotovoltaico, donde la disipación de calor es muy superior al resto del panel. Esto puede ocurrir cuando una célula o varias células están parcialmente sombreadas, presentan microfisuras o una mala conexión eléctrica. Al suceder esto, estas células afectadas se comportan como una carga y generan calor resistivo.
Las causas principales se deben a resistencias elevadas por malas soldaduras y bus-bars (calentamiento por efecto Joule), fallos de diodos de bypass en la caja de conexiones y desajustes (“mismatch”) entre células conectadas en serie.
Pueden detectarse con termografías, curvas I-V y electroluminiscencia.
2. Microrroturas
Las microrroturas o microfisuras son grietas microscópicas en las células o en las interconexiones de las células solares. Estas se pueden formar tras el corte del wafer (oblea) o por tensiones mecánicas/ térmicas durante fabricación (células cada día más finas, 130µm), durante el funcionamiento del panel (por las variaciones de temperaturas noche/día), transporte o instalación.
Aunque son invisibles a simple vista en sus fases tempranas, pueden reducir la generación energética en un 42,8% o más y favorecer la aparición de nuevos puntos calientes.
Pueden detectarse con termografía, curvas I-V y electroluminiscencia.
3. Destrucción del Tedlar
La destrucción del Tedlar consiste en la degradación del backsheet (lámina posterior de Tedlar del módulo) que aísla eléctricamente el módulo. Cuando el encapsulado se degrada, la humedad y el oxígeno penetran en el interior del panel, provocando cortocircuitos, corrosión de las interconexiones y fallo total del módulo, dejándolo inservible.
Las causas principales son la exposición prolongada a radiación UV, ciclos térmicos y humedad sin la protección adecuada, y la presencia de hot-spots que aceleran la degradación del polímero.
Para prevenirlo puedes seguir las siguientes recomendaciones.
- Comprar paneles con backsheets de grado industrial (TPT A) y encapsulantes con estabilizadores UV certificados.
- Utilizar paneles solares con control estricto del proceso de laminación (presión, temperatura y tiempo) para asegurar la adhesión y evitar huecos.
- Utilizar módulos sometidos a pruebas aceleradas de calor húmedo (Damp Heat, IEC 61215-2:2021) y ensayos de adherencia (“peel test”) tras la fabricación.
4. Deslaminado de las células solares
El deslaminado se produce cuando las capas del módulo (vidrio, EVA, célula y backsheet) se separan parcial o totalmente, creando burbujas y pérdidas de aislamiento que dejan al panel expuesto a agentes externos y reducen drásticamente su rendimiento, incluso hasta inutilizarlo.
Suele originarse por ciclos de laminación incompletos o acelerados (temperatura o presión insuficiente) en líneas de producción de calidad media-baja, donde se acortan los tiempos para incrementar el ritmo de fabricación y reducir costes.
Para mitigar ese problema se pueden tomar las siguientes medidas.
- Exigir a los fabricantes control de humedad residual del EVA (< 0,2%) y aplicación de los parámetros adecuados de temperatura y presión durante todo el ciclo de laminado.
- Hacer inspecciones post-laminado con electroluminiscencia o fotoluminiscencia para detectar separaciones incipientes.
- Realizar ensayos acelerados de Damp Heat (IEC 61215-2:2021) para verificar la estabilidad del encapsulado frente a temperatura y humedad antes del envío e instalación.
5. Problemas con los diodos de bypass
Los diodos de bypass vienen instalados en la caja de conexiones de los módulos para derivar la corriente cuando una parte de las células del panel están sombreadas o presentan desajustes eléctricos (mismatch).
Al conducir la corriente en estas condiciones, el diodo puede disipar grandes cantidades de calor (llegando a 100 °C) y, si falla, deja de proteger la sección sombreada, generando puntos calientes que pueden fundir el encapsulado o incluso provocar incendios y dejar el panel inoperativo.
Las causas más frecuentes de fallo son el uso de diodos de baja calidad, cajas de conexiones mal selladas que permiten la entrada de humedad y ciclos térmicos repetidos por sombras recurrentes que terminan con el ciclo de vida del diodo.
Para prevenirlo puedes seguir las siguientes recomendaciones.
- Preguntar siempre al fabricante o instalador por diodos de bypass “tipo militar” o de grado industrial, diseñados para soportar ciclos térmicos extremos y corrientes elevadas.
- Comprobar que la silicona o resina de encapsulado de la caja de conexiones cubre completamente los diodos.
- Hacer inspecciones termográficas periódicas (IEC 62446-3) para detectar diodos al límite de su vida útil y reemplazarlos antes de que se quemen.
6. Amarillamiento del EVA
El amarilleamiento del EVA (etileno-acetato de vinilo que encapsula las células) consiste en su oxidación y degradación que provoca una tonalidad amarillenta. Esto reduce la transmisión de luz, fomenta la aparición de microgrietas y favorece la entrada de humedad, acelerando la pérdida de rendimiento y el riesgo de deslaminado.
Se debe principalmente a la falta de estabilizadores UV en encapsulantes de baja calidad, a un secado insuficiente del polímero antes del laminado y a ciclos de calor húmedo repetidos.
Para evitarlo puedes seguir las siguientes recomendaciones.
- Exigir EVA certificado con estabilizadores UV de última generación y contenido de humedad residual inferior al 0,2%, o bien el uso de POE como encapsulanate, más resistente a este problema.
- Verificar que el panel ha superado ensayos acelerados de calor húmedo y “peel test” tras el proceso de laminado.
7. Soldaduras defectuosas
Las soldaduras defectuosas aparecen cuando las uniones entre bus-bars, ribbons o diodos dentro de la caja de conexiones no están bien hechas (temperaturas de soldadura demasiado bajas, limpieza insuficiente o falta de control de tiempo y presión). Esto genera resistencias localizadas elevadas que provocan puntos calientes, pérdida de potencia y, en casos extremos, grietas en las interconexiones o incluso riesgo de incendio.
Para prevenirlas puedes seguir estas recomendaciones.
- Utilizar paneles solares que NO usen soldaduras.
- Realizar inspecciones periódicas con electroluminiscencia o termografía.
8. Corrosión
La corrosión consiste en la oxidación de contactos metálicos (como bus-bars, ribbons, bornes de la caja de conexiones) elevando la resistencia en serie del módulo. Esto reduce la corriente de cortocircuito y el voltaje en circuito abierto, provocando caídas de rendimiento de hasta un 10 % y, en casos severos, fallo eléctrico completo.
Se produce principalmente cuando la humedad penetra a través de un backsheet agrietado o una caja de conexiones mal sellada, y esto provoca que ocurran reacciones electroquímicas que corroen el cobre, estaño o aleaciones internas.
Para evitarlo puedes seguir las siguientes recomendaciones.
- Someter los módulos a pruebas de Damp Heat (85 °C/85% HR, IEC 61215-2) antes del envío y realizar verificaciones de estanqueidad tras la instalación.
- Hacer revisiones regulares con termografía y trazado de curvas I-V para identificar incrementos lentos en la resistencia en serie y actuar antes de que la degradación sea irreversible.
9. Efecto PID
La degradación inducida por potencial (PID) ocurre cuando existe una diferencia de voltaje entre las células solares y otros componentes del módulo (por ejemplo, el marco metálico o el vidrio), lo que provoca la migración de iones (principalmente sodio) hacia la superficie de la célula y la formación de corrientes parásitas que incrementan localmente la temperatura y deterioran el recubrimiento antirreflectante. En ambientes húmedos y cálidos, este fenómeno puede reducir la potencia del módulo en más de un 30 %.
Las causas principales son el alto voltaje de sistema (por encima de 600V), un marco conectado a tierra sin aislamiento adecuado y la presencia de humedad que facilita el transporte iónico.
Para mitigar la PID puedes seguir las siguientes recomendaciones.
- Utilizar módulos certificados como resistentes a PID, certificados según IEC TS 62804-1 (96 h a 60 °C, 85% HR, hasta 1.000V).
- Asegurar una conexión a tierra optimizada (minimizando la diferencia de potencial entre células y chasis).
10. Pérdidas por calor húmedo
Las pérdidas por calor húmedo consisten en la degradación acelerada de módulos bajo condiciones de calor y humedad elevada. Un estudio de la Universidad de Nueva Gales del Sur expuso paneles TOPCon, HJT y PERC a 85 °C y 85% de humedad relativa durante 1 000 h (IEC 61215-2, prueba 10.13). Mientras que los PERC apenas sufrieron daños, los TOPCon y HJT mostraron pérdidas de potencia del 10 al 16 %.
Este fallo se debe a que la humedad y el calor promueven reacciones químicas con contaminantes (Na, Ca, Mg, Cl, S) que aumentan la recombinación en las uniones HJT (reduciendo Voc e Isc) y corroen contactos metálicos en TOPCon (incremento del 41 % en la resistencia en serie).
Para evitarlo puedes seguir algunas de estas recomendaciones.
- Someter todos los módulos a ensayos acelerados de Damp Heat (IEC 61215-2) y “peel test” post-laminado para verificar la estabilidad frente a calor y humedad.
- Garantizar un sellado hermético de la caja de conexiones.
11. Roturas de Vidrio
Los módulos fotovoltaicos actuales de vidrio-vidrio presentan tasas altas de rotura (entre 5% y 10% en los primeros dos años), especialmente cuando utilizan un vidrio trasero muy fino (aproximadamente 2 mm).
Estas roturas se deben a tensiones mecánicas y térmicas derivadas de imperfecciones microscópicas en la fabricación o manipulación, tensiones internas por presiones desiguales en la laminación y diferencias significativas en resistencia entre el vidrio delantero templado y el trasero semitemplado.
Además, los módulos más grandes incrementan estas tensiones internas, lo que facilita aún más las fracturas bajo condiciones de carga como viento o nieve, y ante variaciones rápidas de temperatura.
A pesar de estos problemas, el mercado actual sigue dominado por paneles solares de doble vidrio debido principalmente al factor coste. En productos de gama baja, el vidrio solar semitemplado de 2 mm resulta más económico (aproximadamente entre 0,99 y 9,99 dólares por m²) que los backsheets de polímero tipo Tedlar (entre 1,00 y 4,00 dólares por m²). Esta diferencia en coste, aunque pequeña, ha sido suficiente para impulsar el uso generalizado del vidrio semi templado en la parte posterior de los módulos fotovoltaicos, a pesar de los riesgos asociados a su menor resistencia frente a impactos y estrés térmico.
Para evitarlo, asegúrate que el vidrio trasero sea más grueso que 2 mm o utiliza paneles con backsheets de Tedlar.
¿Se pueden reparar las placas solares dañadas?
Sí, pero depende del tipo de avería. Algunas, como las microfisuras leves, sí pueden abordarse mediante técnicas de recableado y sellado. Otras, como el deslaminado o la rotura de vidrio, suelen ser irreparables y obligan a sustituir el módulo.
En detalle podemos resumirlas en la siguiente lista.
- Microfisuras leves: se pueden reparar reforzando las conexiones con puentes de soldadura conductiva y sellando las grietas con resinas UV especiales para restaurar la continuidad eléctrica y proteger frente a humedad.
- Fallos en diodos de bypass o corrosión de bornes: reemplazando el diodo defectuoso o el conector corroído y volviendo a sellar la caja de conexiones con resina siloxánica de grado industrial, se recupera la función original sin necesidad de reemplazar el panel completo.
- Deslaminado o destrucción del backsheet (Tedlar): una vez que el encapsulado se separa o el polímero se fragmenta, la húmedad penetra y corroe internamente; el panel queda inservible y no resulta económicamente viable repararlo.
- Rotura de vidrio: las fisuras o fracturas del vidrio templado comprometen la estanqueidad y la seguridad; en la práctica es preciso cambiar el vidrio completo o el módulo, ya que el coste de reemplazo suele superar el 80% del valor del panel y las reparaciones parciales no garantizan rendimiento ni durabilidad.
¿Las averías de los paneles solares dependen de su calidad?
Sí, la calidad del BOM (coste de los materiales), la precisión en la fabricación y el rigor de la certificación reducen drásticamente la tasa de defectos de los módulos, ya que componentes de calidad inferior incrementan riesgos de degradación prematura.
Según Asier Ukar de Kiwa PI Berlin y el PVEL Scorecard, los fallos a nivel de BOM pasaron del 32% en 2023 a un 41% en 2024, y el 66% de los fabricantes registraron defectos en las pruebas de fiabilidad, reflejo de la intensa presión sobre precios que ha debilitado los controles de calidad en líneas de montaje. Además, la guerra de precios entre 2022 y 2024 ha llevado a sacrificar espesores de células, estabilizadores UV en EVA y estándares de soldadura, incrementando la incidencia de microfisuras y otros mecanismos de degradación temprana.
¿Cuál es el estado actual de la calidad de las placas solares?
Entre 2022 y 2024, la industria solar experimentó un crecimiento sin precedentes (199 GW instalados en 2022, 345 GW en 2023 y 593 GW en 2024) y una competencia feroz con una caída de precios de más de un 50%, pero también aumentó la preocupación por la calidad de los módulos fotovoltaicos (FV).
Incluso los fabricantes Tier 1 (las marcas con supuestamente mayor solvencia) experimentaron problemas de calidad, desde defectos de fabricación hasta problemas de rendimiento.
De hecho los directores generales de fabricantes de paneles solares dieron la voz de alarma sobre el hecho de que la rápida caída de los precios y las nuevas tecnologías estaban comprometiendo la calidad.
Además de esto, la asociación CEA (Clean Energy Associates) constató en el año 2023 el enorme incremento de averías por microfisuras en células y en las interconexiones como se aprecia en la siguiente gráfica.
Las pruebas de rendimiento juegan en tu contra para reclamar garantías
Un problema añadido a la pérdida de calidad de los paneles solares desde el año 2022, y que se ha ido incrementando posteriormente, es que las máquinas de medición de potencia, que se utilizan para clasificar los paneles solares en fábrica, tienen un margen de error de +/-3%, es lo que se denomina “incertidumbre de medida” (diferencia entre la potencia real y la nominal que es por la que pagas el panel).
De este modo, si un panel solar muestra una potencia real de un -3% de la que se menciona en la ficha del fabricante, está dentro del margen de incertidumbre de medida y no tienes derecho a reclamar garantías.
Como ejemplo, Gerhard Meyer, director del laboratorio Spire Solar Iberia, realizó un ensayo con varios paneles solares con potencia pico declarada de 315 Wp. En el ensayo se comprobó que el 100% de los paneles ensayados estaban en el rango negativo de la incertidumbre de medida.
Muchas son las voces de sector fotovoltaico que remarcan la innegable pérdida de calidad de los módulos fotovoltaicos los últimos dos años, de los que resumimos los siguientes.
- Kiwa PI Berlin: Los laboratorios de pruebas fotovoltaicas han observado más defectos a medida que los fabricantes reducen costes. «Los países que han experimentado un rápido aumento de la capacidad de fabricación en los últimos tiempos han tenido dificultades con el control de calidad, como revelan las mayores tasas de defectos», informó Matthew Lu, vicepresidente de Kiwa PI Berlin. Esta rápida expansión no alineada con la demanda real del mercado, y la competencia de precios ha dado lugar a fallos de calidad.
- Del mismo modo, Asier Ukar, de la Kiwa Berlin Spain, advirtió a mediados de 2023 que las nuevas tecnologías de alta eficiencia (TOPCon) se estaban implantando de forma precipitada. Indicó el hecho de que los fabricantes “no eran plenamente conscientes de los diferentes mecanismos de degradación al pasar de PERC a TOPCon”
- Fraunhofer ISE: los datos del Instituto Fraunhofer de Alemania comprobaron una caída en el rendimiento de los paneles con respecto a las especificaciones de los fabricantes, demostrando que se ha comprometido la calidad. Entre 2012 y 2016, los módulos probados alcanzaron o superaron de media la potencia nominal, pero entre 2020 y 2023 se produjo una desviación negativa del rendimiento. Un informe del año 2024, comprobó desviación negativa... de alrededor del 1,3% de lo que declaran los fabricantes, según Daniel Philipp del Instituto Fraunhofer.
- Zhong Baoshen, de Longi Green Energy Technology, expresaba como se están sacrificando la calidad de los paneles solares para reducir sus costes.
- PVEL Scorecard declaró que los informes de fiabilidad del sector han sufrido un aumento de los fallos en los módulos coincidiendo con una intensa presión sobre los precios. Concretamente se registró el porcentaje más alto de fallos en los módulos en sus diez años de historia. El 66% de los fabricantes tuvieron fallos en las pruebas de 2024, y los fallos a nivel de la lista de materiales pasaron del 32% de las muestras en el informe de 2023 al 41% en 2024.
¿Por qué comprar paneles solares de calidad?
Invertir en módulos de alta calidad como los representados por SunFields (FuturaSun y REC), garantiza un rendimiento fiable a lo largo del tiempo, reduce notablemente los costes de operación y mantenimiento gracias a una menor degradación, y poseen una garantía de al menos 25 años tanto de producto como de producción, así como una mayor resistencia contra las averías más comunes de los paneles solares.
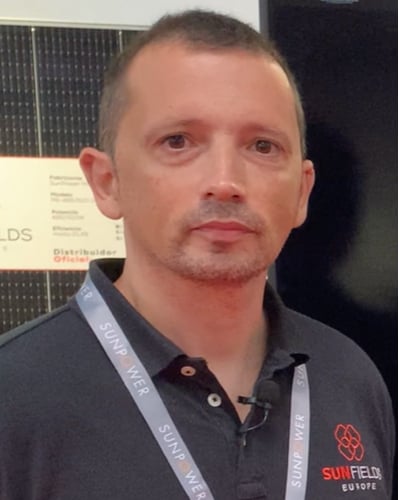
José Alfonso Alonso Lorenzo
Profesional Fotovoltaico desde 2006.
- Ingeniero técnico Industrial por la Escuela Politécnica de Ferrol.
- Experto en Solar Fotovoltaica por el Centro de Investigaciones Energéticas, Medioambientales y Tecnológicas de Madrid en 2009-2010.
- Experto Profesional en Energía Fotovoltaica, por la UNED 2010-2011.
- Gerente y Responsable de Compras en SunFields Europe desde 2010.
Más sobre mí en: https://es.linkedin.com/in/jose-a-alonso-sunfields/